How Five-Axis CNC Machines Reduce Production Time
In today’s fast-paced manufacturing environment, reducing production time without compromising quality is essential. The five-axis CNC machine is one of the most significant advancements aiding this goal. Unlike traditional three-axis machines operating on the X, Y, and Z planes, five-axis CNC machines introduce two additional rotary axes, offering greater flexibility and precision.
Here are a few ways this cutting-edge technology drastically reduces production time for manufacturers across various industries:
1. Eliminating Multiple Setups
Traditional CNC machines often require several setups to complete a complex part. Each time a part needs to be reoriented for different cuts, the production halts, leading to downtime. With five-axis CNC machines, the additional rotational axes allow the part to be machined from nearly all angles in one setup. This means fewer interruptions and faster turnaround times.
By eliminating multiple setups, manufacturers also reduce the risk of human error in part alignment, further speeding up production by minimizing the need for corrections and quality control issues.
2. Handling Complex Geometries in a Single Operation
Complex parts with detailed geometries often need multiple operations on traditional machines, with each one taking time to plan and execute. Five-axis machines simplify this by allowing operators to machine complex surfaces and features in a single operation. The ability to maneuver the cutting tool freely around the part ensures that even the most complicated designs can be handled efficiently.
This versatility eliminates the need to move the part between multiple machines or orientations, saving time and labor costs, and reducing the potential for production bottlenecks.
3. Improved Cutting Speeds and Efficiency
The enhanced precision and control offered by five-axis CNC machines enable manufacturers to optimize cutting paths and tool angles. This reduces the time spent on each part while maintaining high-quality standards. In addition, improved cutting angles mean better tool engagement, allowing for faster material removal rates.
Since five-axis machines can machine parts from multiple angles without stopping, they reduce idle time and optimize material flow. This streamlining of the production process further accelerates the manufacturing cycle.
4. Reduced Lead Time for Prototyping and Custom Orders
Five-axis CNC machines are also invaluable for manufacturers who deal with prototyping or small custom orders. With traditional machines, creating a prototype or fulfilling a custom order involves lengthy setup times, especially for complex parts. Five-axis machines reduce the time spent on setup and production, allowing manufacturers to bring prototypes or custom parts to market faster.
For industries where time-to-market is critical, such as aerospace, automotive, or medical device manufacturing, this reduction in lead time can make all the difference in staying ahead of the competition.
5. Better Surface Finishes, Fewer Secondary Operations
Another way five-axis CNC machines save time is by producing better surface finishes, eliminating the need for secondary operations like grinding or polishing. By achieving tighter tolerances and smoother finishes during the initial cutting process, manufacturers can skip additional steps and reduce production time and costs even further.
Five-axis CNC machines are revolutionizing the manufacturing industry by offering enhanced flexibility, precision, and efficiency. Investing in five-axis CNC technology is a smart move for manufacturers looking to boost productivity and reduce costs.
Content for MagPie Machining by Minieri & Company, LLC, Copyright © 2019-2025, All Rights Reserved.
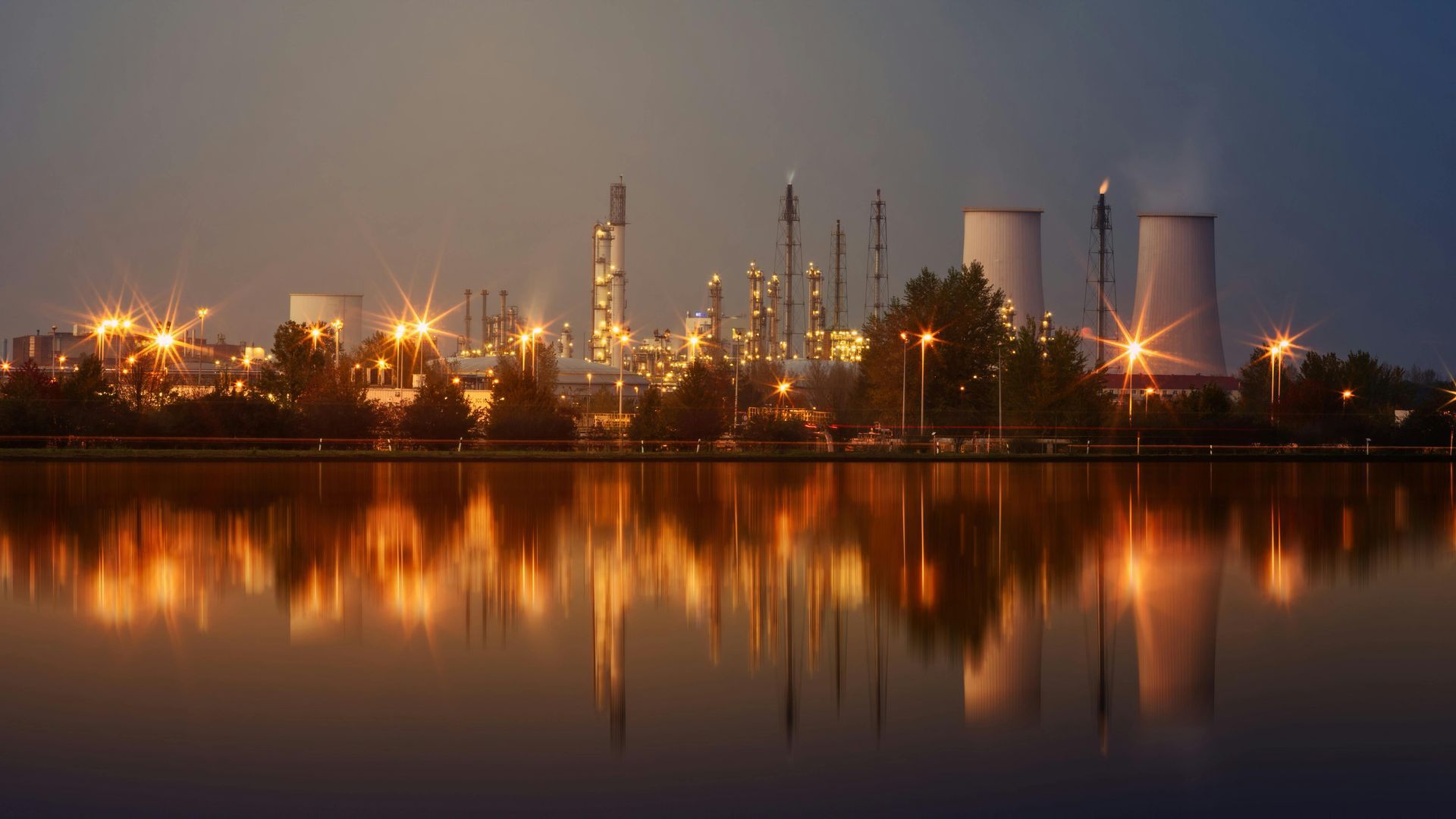
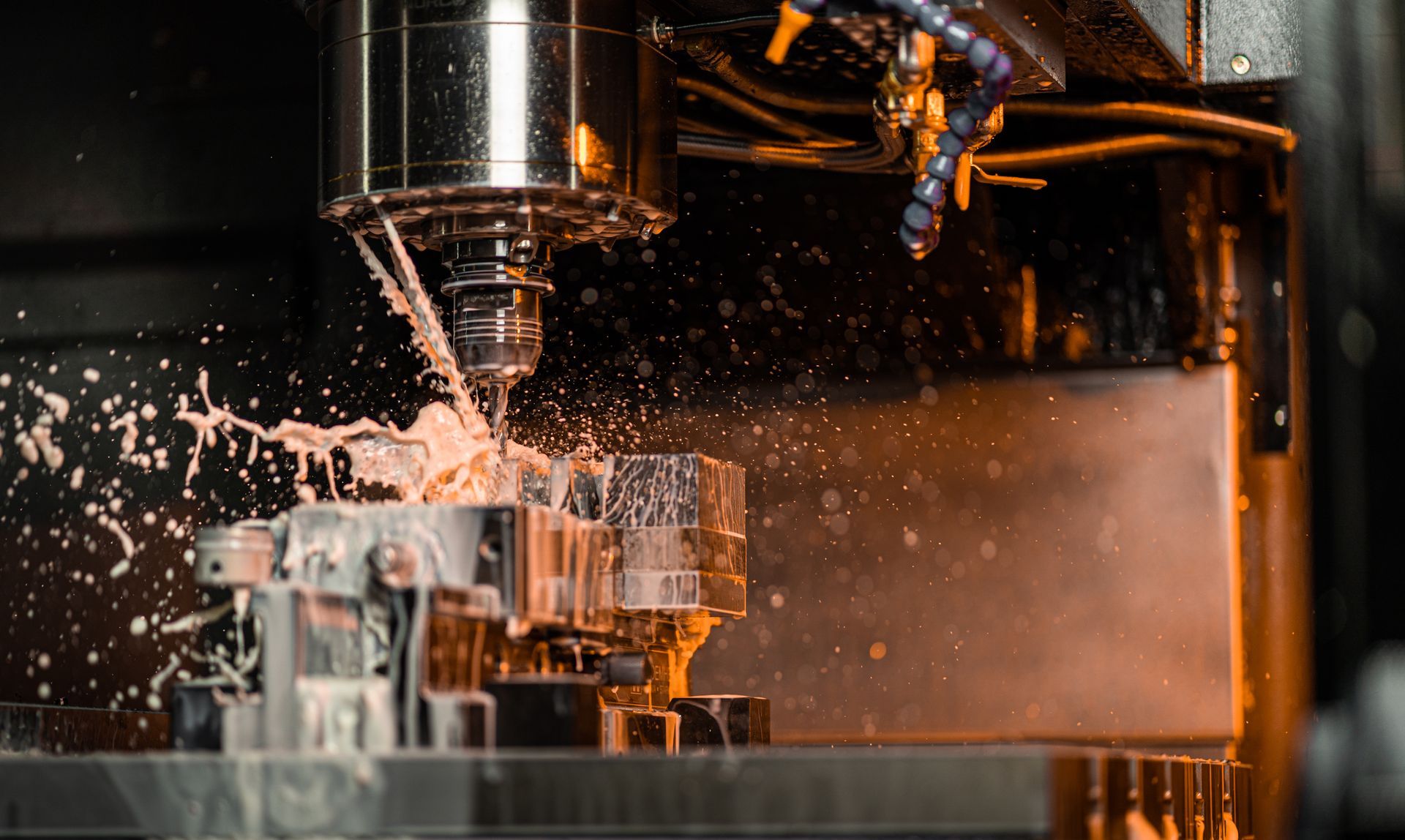